金屬增材制造是指使用金屬粉末逐層生產3D零件的技術。該方法使得能夠生產工業零件的復雜結構,否則將無法通過傳統方法來制造。Eplus3D提供先進的金屬3D打印解決方案,為企業和小型企業帶來更高的生產率,產品質量和工作效率。 不同行業的應用
金屬致癮制造業的持續發展已將其應用擴展到了廣泛的行業,包括航空航天,汽車,工具,醫療保健,牙科,消費品,教育等。
金屬增材制造的應用包括零件生產,快速成型,夾具和夾具,產品定制,注塑成型,醫療設備等。
以下示例演示了這些金屬3D打印應用中的一些應用
工業。
鈑金制造廣泛用于電氣和電子,汽車,電信,醫療等行業。鈑金是支撐和成型汽車,計算機或手機等產品的骨架。
鈑金零件的設計和制造成為多樣化但小批量生產的趨勢,成為新產品開發的關鍵步驟。
常規的鈑金制造過程采用沖壓模具進行生產。以汽車鈑金零件為例,其成型過程是通過沖模,切割模,成型模,分離模,壓模,彎曲沖頭等進行的。制造新模的加工過程既昂貴又費時,而不是適用于小批量快速生產鈑金零件。
關于小批量鈑金零件生產,許多鈑金工廠都采用了激光切割結合CNC彎曲技術的方法。與傳統的沖模成型工藝相比,該方法不需要工具加工,節省了成本,并且周期短,可以快速制造結構簡單的鈑金。
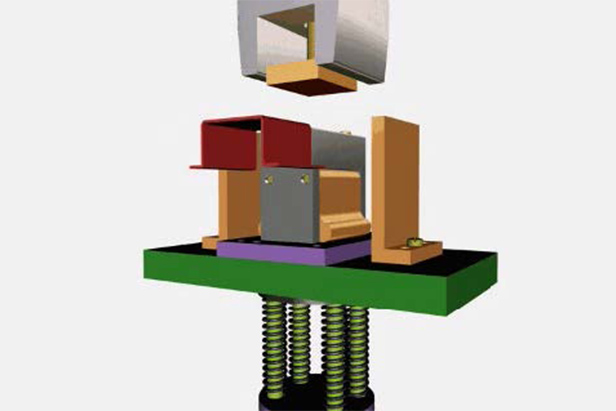
阻止工件彎曲
阻止工件彎曲
但是,激光切割只能用于成形,孔切割,而彎曲只能用于平面結構。該技術不適用于具有彎曲表面或凹凸表面的異型板材的生產。
小批量生產汽車座椅鈑金件
來自中國的汽車座椅制造公司,專門從事汽車座椅的開發,生產和銷售,已成為長安,吉利,福特和長城等汽車工廠的主要承包商。他們將在一周內展示一些新的汽車座椅解決方案,但是用于核心鈑金零件的工具仍在開發中,因此無法生產鈑金零件。
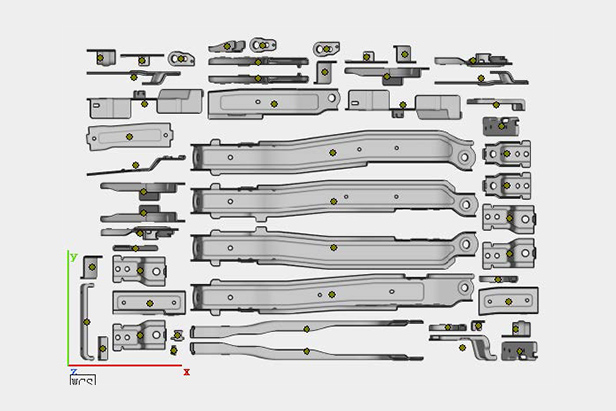
鈑金零件設計圖
鈑金零件設計圖
該汽車座椅套由78個零件組成,厚度為1.5 – 2.5 mm。大多數零件具有肋和凹凸結構。因此,無法通過激光切割加上CNC彎曲來形成零件。受CNC銑刀的限制,某些角部區域也無法完全恢復為銑床制造的原始設計。順便說一句,銑削本身并不是生產零件的非常有效的過程。
Eplus3D將挑戰任務分配給了位于中國重慶的專業3D打印服務中心之一,該中心專門研究金屬,為上述汽車座椅鈑金生產提出了3D打印解決方案。經過數據分析后,選擇316L不銹鋼作為生產材料,并使用研磨對表面進行拋光。在短短7天內,完整的座椅鈑金零件就交付了,由3個Eplus3D金屬打印機EP-M250生產,他們完美地再現了原始設計。
3D打印的鈑金零件
在上述情況的基礎上,對3D金屬打印,柔性鈑金制造和其他小批量鈑金制造技術進行了比較:
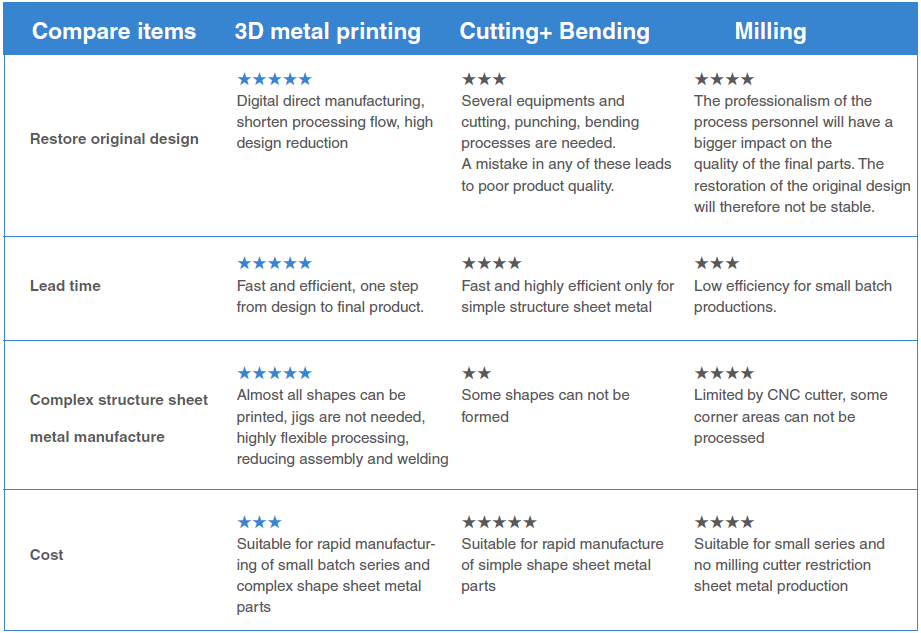
Comaprison 3D金屬印刷,柔性鈑金制造和其他小批量鈑金制造技術
讓我們看看另一個案例,以更全面地了解用于靈活生產的金屬3D打印。
一家機器制造商希望生產一種消音器,該消音器由四個組件組成,對于中等結構區域,它們的均勻外殼厚度為0.73毫米,均勻厚度為0.6毫米。
消音器
四個消音器組件的鈑金結構很復雜。它不能通過切割和彎曲來生產。薄的壁厚使其無法通過銑削生產。只有兩個選項。一種是打孔,另一種是3D打印。
用沖壓工具生產的零件具有很高的精度,并且可以高度還原原始設計。但這需要打孔工具,這在生產中非常耗時且昂貴。
借助金屬3D打印的優勢,從數據處理到產品交付僅需3天,并且設計細節得以充分體現。
最后,該客戶選擇了Eplus3D重慶3d打印服務中心來完成任務。Eplus3D EP-M250用3d打印的金屬片可以達到0.1mm的尺寸精度。越來越多的案例證明3d打印技術可以使零件保持高質量,并大大降低產品成本并縮短交貨時間。
行業期望
鈑金制造是世界上發展最快的行業之一。顯然,金屬薄板制造中的柔性生產是產品多樣性和小批量產品需求增長驅動的趨勢。越來越多的鈑金加工公司受益于增材制造技術,從而為客戶創造了更多價值,例如減少了組裝步驟,極大的設計自由度以及時間和成本的最小化。
EP-M250 Pro
雙激光3D打印機(金屬粉末床融合)
EP-M250 Pro
EP-M250 Pro是使用先進的金屬粉末床融合(MPBF)技術的雙激光金屬3D打印機。它能夠輕松快速地將CAD數據轉換為高性能,復雜結構的金屬零件。3D打印機是中型零件和小批量生產的理想選擇。